塑木复合材料是采用木材加工剩余物、森林抚育剩余物、废旧木材、农作物秸秆等木质纤维材料(35%~70%)和废旧热塑性塑料(主要为PE、PP、PVC)为主要原料,通过挤出、压制等成型方式形成的复合材料。塑木复合材料既具有木质纤维材料的高强度和高弹性,又具有塑料的高韧性和耐疲劳等优点,是一种既似木材又优于木材的新型代木材料。木纤维是吸水性较强的材料,一般含水量在15%甚至更高,无机填料也达到5%左右,而水含量的高低是影响塑料特别是塑木生产稳定性和制品质量的天敌,会响发泡倍率、制品的吸水率、制品的变形、制品的耐候性和其他物理性能。所以水分最好控制在1%以内。

控制好合理水分的纤维和填料 →加入高混机里 →混到100℃ →加入适量的偶联剂 →混到110~115℃ →关掉马达,停止时打开混合机大盖2~3分钟 →加入PVC和稳定剂 →混到80℃ →加润滑剂及其他助剂 →到100℃时加入加工助剂,发泡剂 →120~125℃时卸粉 →粉卸完后马达停止了再打开大盖,2~3分钟后再混下一手料(最好混五手料,清理一次混合机) → 粉在冷拌桶里冷却到40℃ →造粒或加入双螺杆生产(冷拌桶务必有循环冷却水)。1、在混料时必须注意观察温度和时间,如一般冷锅混一手料在20-25分钟左右,热锅在12~15分钟左右(温度设定125℃左右),如果时间有相差3分钟或更长,可能是感温线有问题或温控不准,或混合机牛角刀磨损严重,会影响发泡倍率的稳定和产品颜色。3、主机电流的大小和稳定性。如主机电流波动较大说明滑剂、加工助剂、纤维与PVC各组分之间分散不是很均匀。4、烘干机的温度一般设定在60-80℃之间,且经常保持在桶的容积的80%左右,这样有利于生产和颜色的稳定,提高制品的表观质量。5、单螺杆挤出机主要靠摩擦输送物料,混炼效果差,木粉在机筒中停留时间长,易烧焦。因此,在PVC/塑木复合材料挤出中受到较大的限制。为了提高PVC/塑木的混合效果,用于PVC/塑木加工的单螺杆应该设混炼区,或者先造粒,然后用粒料挤出成型,但这个过程消耗了助剂,降低了PVC性能。
参考配方
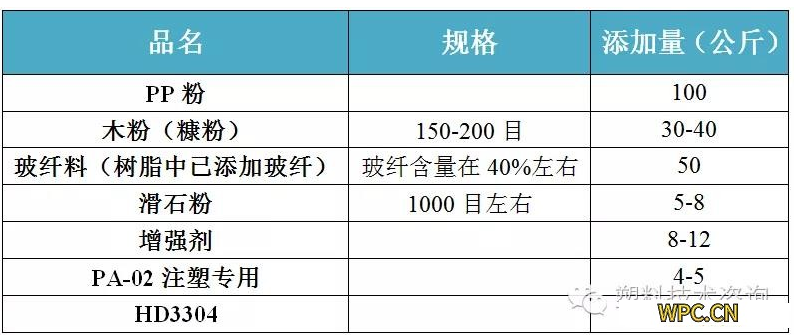
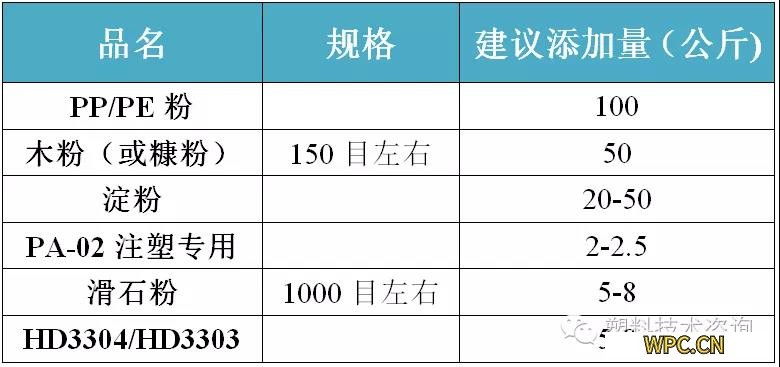
1、其中抗氧剂的添加量和淀粉的添加量据降解时间的长短来定,此配方环保达到食品级可用于餐具,化妆品包装,产品力学性能好,冲击强度高;2、不同的产品、不同的使用用途、以及产品的不同大小厚度,在木粉及其它的无机物或纤维的添加量上都不一样,如塑木注塑工艺品因其是用来观赏的产品对力学指标要求不高且产品小所以填充可加到100%。1、提高了填料(木粉、糠粉、无机物)的分散性,且添加量少,用于挤出为2.0%左右,用于注塑比挤出增加10~30%;2、优异的流动性,大幅提升产能,树脂与木粉和无机物的比例是1:3左右,用于塑木注塑在填料的添加量和产品表面及力学性能等方面效果很好,不会析出表面;3、具有优异的偶联功能,加此助剂无需加偶联剂,提高了产品的力学性能,如弯曲强度、弯曲模量、冲击强度等,降低含水率及吸水率(冲击强度比用硬脂酸、石蜡、PE蜡润滑体系高400~800牛,吸水率低30%);
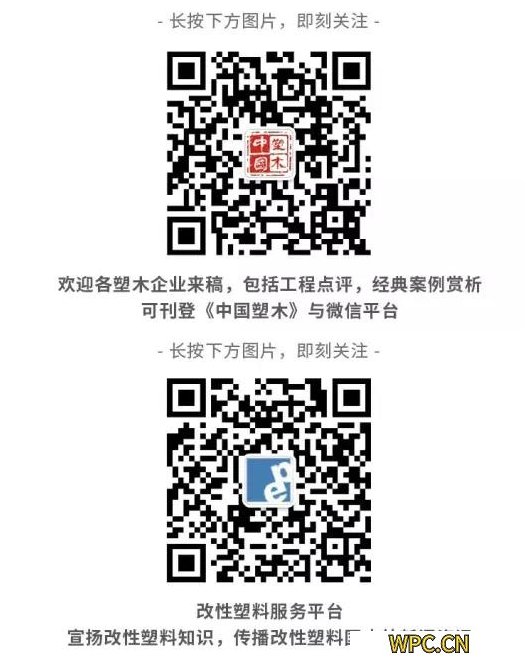